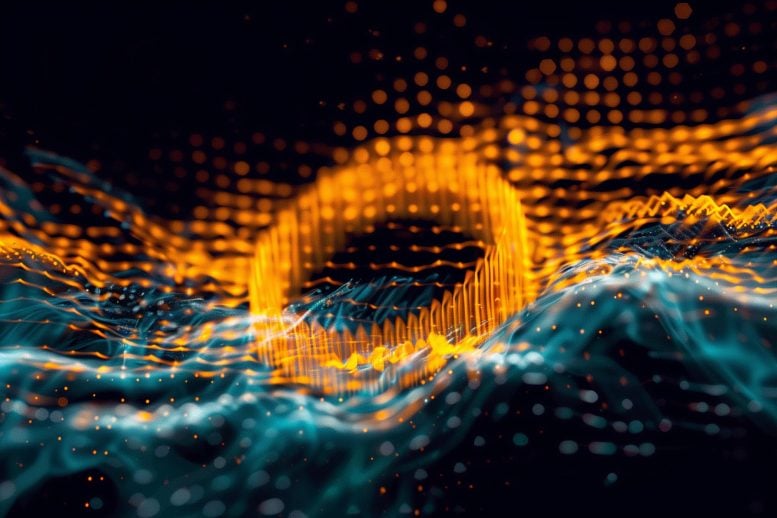
Researchers have developed a soft, flexible material with adaptive durability that strengthens upon impact, suitable for wearable technology and medical sensors. Credit: SciTechDaily.com
A new flexible, electricity-conducting material mimics the adaptive strength of cornstarch slurries, offering promising applications in wearable and medical sensor technology.
Accidents happen every day, and if you drop your smartwatch, or it gets hit really hard, the device probably won’t work anymore. But now, researchers report on a soft, flexible material with “adaptive durability,” meaning it gets stronger when hit or stretched. The material also conducts electricity, making it ideal for the next generation of wearables or personalized medical sensors.
The researchers presented their results today at the spring meeting of the American Chemical Society (ACS). ACS Spring 2024 is a hybrid meeting being held virtually and in person March 17-21; it features nearly 12,000 presentations on a range of science topics.
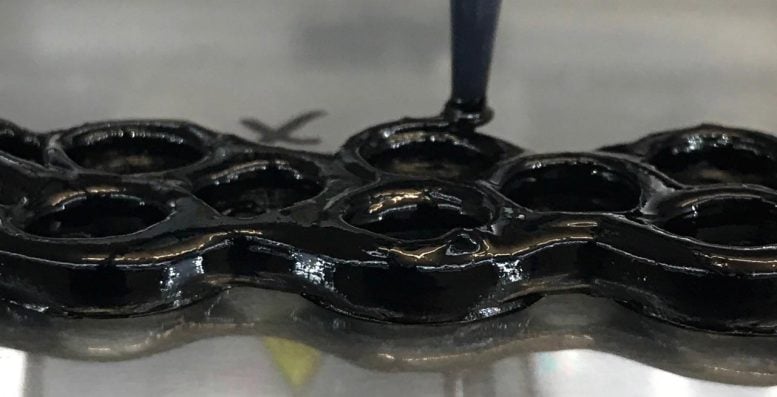
This flexible and conductive material has “adaptive durability,” meaning it gets stronger when hit. Credit: Yue (Jessica) Wang
Inspiration From Cooking Ingredients
Inspiration for the new material came from a mixture commonly used in cooking — a cornstarch slurry.
“When I stir cornstarch and water slowly, the spoon moves easily,” explains Yue (Jessica) Wang, a materials scientist and the project’s principal investigator. “But if I lift the spoon out and then stab the mixture, the spoon doesn’t go back in. It’s like stabbing a hard surface.” This slurry, which helps thicken stews and sauces, has adaptive durability, shifting from malleable to strong, depending on the force applied. Wang’s team set out to mimic this property in a solid conductive material.
Postdoctoral researcher Di Wu talks about a polymer material he is helping to develop that is flexible and becomes tougher, depending on how the body moves.
Development of the Material
Many materials, such as metals, that conduct electricity are hard, stiff, or brittle. But researchers have developed ways to make soft and bendable versions using conjugated polymers — long, spaghetti-like molecules that are conductive. Yet, most flexible polymers break apart if they undergo repeated, rapid or large impacts. So, Wang’s team at the University of California, Merced, set out to select the right combination of conjugated polymers to create a durable material that would mimic the adaptive behavior of cornstarch particles in water.
Initially, the researchers made an aqueous solution of four polymers: long, spaghetti-like poly(2-acrylamido-2-methylpropanesulfonic acid), shorter polyaniline molecules and a highly conductive combination known as poly(3,4-ethylenedioxythiophene) polystyrene sulfonate (PEDOT:PSS). After spreading a thin layer of the mixture and drying it to make a film, the team tested the stretchy material’s mechanical properties.
Enhancing Material Properties
They found that rather than breaking apart from very rapid impacts, it deformed or stretched out. The faster the impact, the more stretchy and tough the film became. And surprisingly, just a 10% addition of PEDOT:PSS improved both the material’s conductivity and adaptive durability. Wang notes that this result was unexpected because, on their own, PEDOT and PSS don’t get tougher with rapid or high impacts.
The four polymers, two with positive charges and two with negative charges, tangle up like a big bowl of spaghetti and meatballs, explains Di Wu, a postdoctoral researcher in Wang’s lab who is presenting the work at the meeting. “Because the positively charged molecules don’t like water, they aggregate into meatball-like microstructures,” says Wu. The team’s hypothesis is that the adaptive behavior comes from the meatballs absorbing the energy of an impact and flattening when hit, but not completely splitting apart.
However, Wu wanted to see how adding small molecules could create a composite material that was even tougher when stretched or dropped quickly. Because all the polymers had charges, the team chose molecules with positive, negative or neutral charges to test. Then they assessed how the additives modified the polymers’ interactions and impacted each material’s adaptive durability.
Preliminary results have indicated that the positively charged nanoparticles made of 1,3-propanediamine were the best additive, imparting the most adaptive functionality. Wu says this additive weakened the interactions of the polymers that form the “meatballs,” making them easier to push apart and deform when hit, and strengthened the tightly entangled “spaghetti strings.” “Adding the positively charged molecules to our material made it even stronger at higher stretch rates,” says Wu.
Advanced Applications and Future Work
In the future, Wang says, the team will shift toward demonstrating the applicability of their lightweight conductive material. The possibilities include soft wearables, such as integrated bands and backside sensors for smartwatches, and flexible electronics for health monitoring, such as cardiovascular sensors or continuous glucose monitors. Additionally, the team formulated a previous version of the adaptive material for 3D printing and produced a replica of a team member’s hand, demonstrating the potential incorporation into personalized electronic prosthetics. Wang thinks the new composite version should also be compatible with 3D printing to make whatever shape is desired.
The adaptive durability of the material means that future biosensor devices could be flexible enough for regular, human motion but resist damage if they’re accidentally bumped or hit hard, explains Wang. “There are a number of potential applications, and we’re excited to see where this new, unconventional property will take us.”
Title
Effect of additives on deformation rate-adaptive conducting polymers
Abstract
Deformation-rate adaptive properties endow polymeric materials with higher strength, elongation at break, and toughness under faster impact. A conductive polymer system consists of two polyelectrolyte complexes, polyaniline:poly(2-acrylamido-2-methyl-1-propanesulfonic acid (PANI:PAMPSA) and poly(3,4-ethylenedioxythiophene):polystyrene sulfonate (PEDOT:PSS), along with 35 wt% propanesulfonic acid (PSA) and 10 wt% water as plasticizers, showed deformation-rate adaptive behavior. Our previous work suggested that the adaptive behavior is likely due to the disintegrating of the micelles formed by hydrophobic PANI and hydrophilic PAMPSA under fast deformation rates, while the additive (i.e., PSA) is hypothesized to tune adaptive behavior via affecting the formation of micelles. To fully decipher the role of additives, the same polyelectrolyte system containing negatively-charged PSA, positively-charged 1,3-propanediamine (13DA), or neutral glycerol (Gly) were investigated. While the rate-adaptive behavior was confirmed by tensile testing in the samples with all the three additives, 13DA showed the greatest improvement of Young’s modulus, tensile strength, elongation at break, and toughness at higher deformation rates. Oscillatory shear and stress-relaxation studies reveal that the deformation-rate adaptive behavior originated from the transient networks formed by the agglomeration of hydrophobic PANI and PEODT segments in our materials. The positively-charged, basic additive, 13DA, could further facilitate the formation of networks by screening the polyelectrolyte interactions and bridging the polyanions. This study unearths the mechanism of deformation-rate adaptive behavior in this model polymer system, and it can be potentially applied on fabricating other novel and robust polymeric materials.
The research was funded by the University of California, Merced; a National Science Foundation CAREER grant; and an Arnold and Mabel Beckman Foundation’s Young Investigator award.